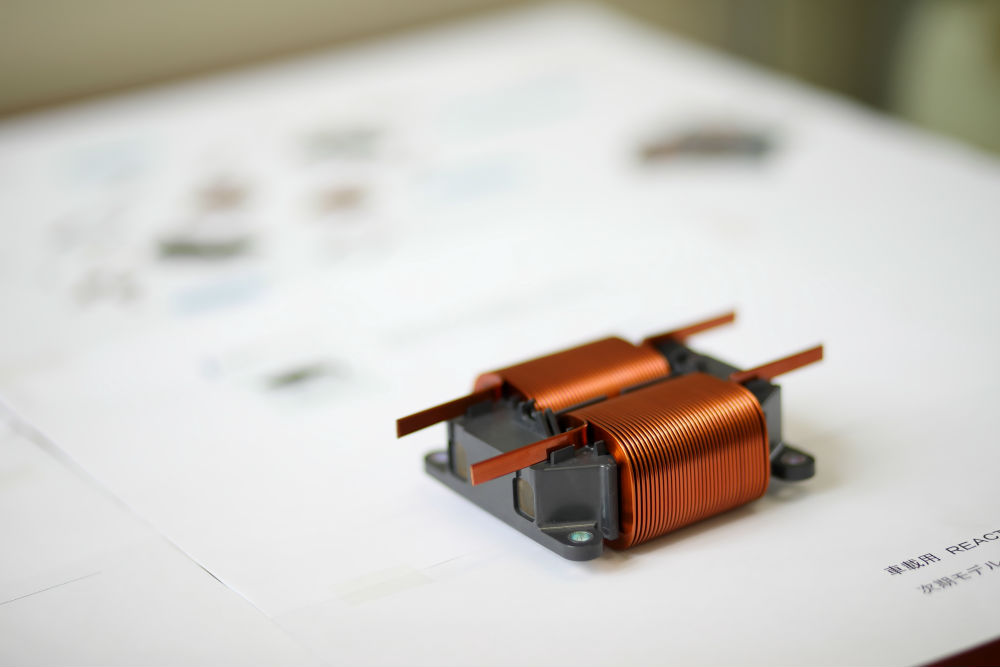
プラスチック成形のエキスパート
プラスチック製品を製造する会社のなかで、スズモト株式会社が他社ともっとも大きく違う点は、金型の設計、製造から最終製品の成形まですべて一貫体制で生産をしているというところだ。これはプラスチック成形品の製造業者としては比較的に少ない体制だ。この体制ができあがったのは、 山形県庄内に大手セットメーカーが進出した1985年ごろ。プラスチックの射出成形で最も大事なツールで、ノウハウのかたまりであり、困難極まる事業であるが、より精密で高品質な製品の生産のために、金型の内製化に踏み切ったという。
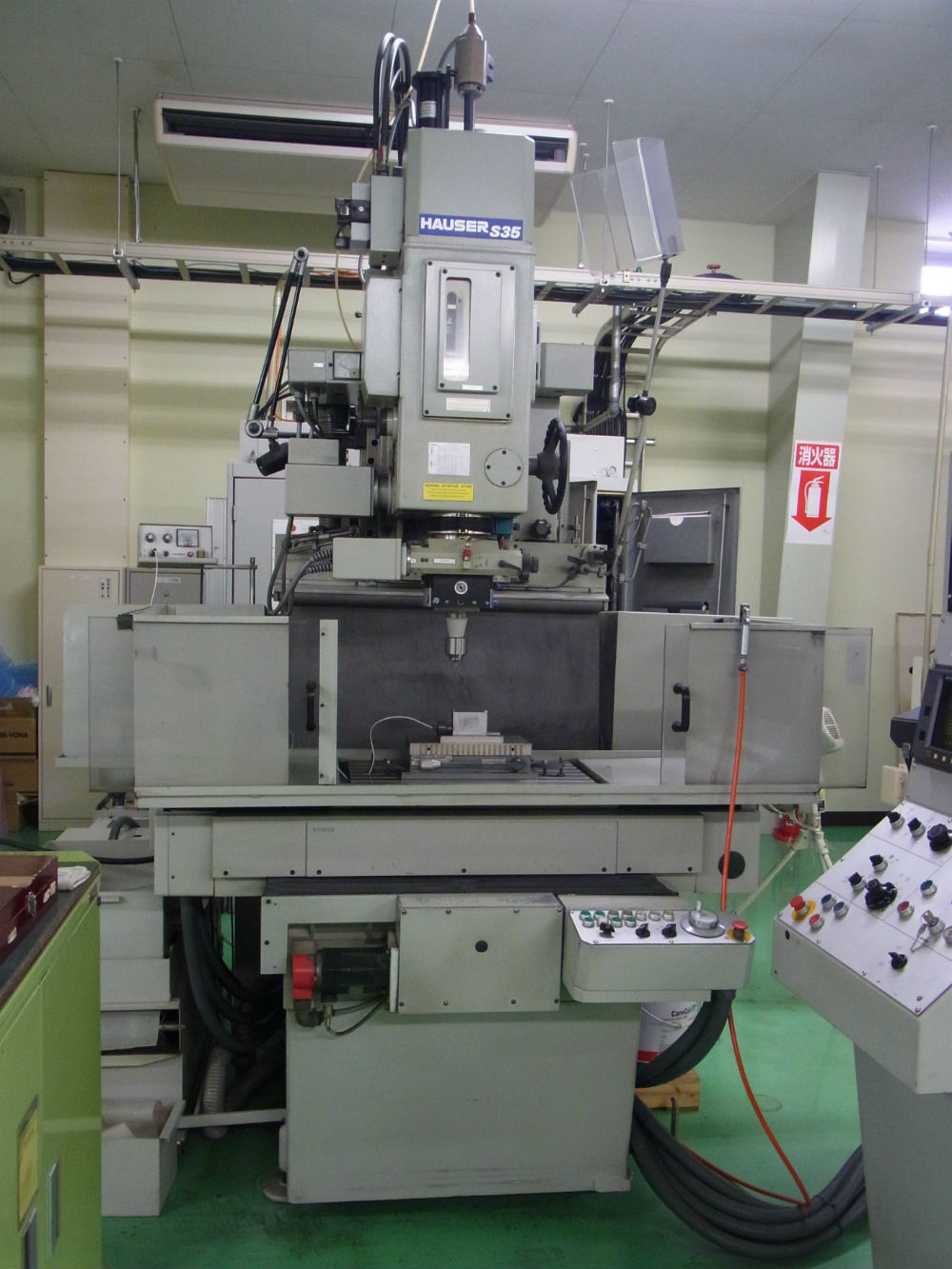
今回インタビューをした金型設計課の櫻井啓太は金型の設計を担当している人物。櫻井は「隣に製造現場があるのでコミュニケーションが迅速。だからすぐに製造側と意見を交えながら改善ができる。そこは仕事をするうえで大きな強みです」という。ときには金型加工の部門や成形の部門から厳しい意見が飛んでくることもある。だが櫻井は「それも先に進むためのひとつのステップ。そこからよりいいものができあがると考えています。それよりもその意見が直接伝わってくることのほうが大事だと感じています」と言う。
また、大阪からUターンで就職し、工程改善を担当している佐藤洋介も「良品をより多く製造するための工程改善は金型、成形の両方から原因を探らなくてはできないので、その双方が社内にあるということは、より横断的で確度の高い考察ができると感じています」と話す。「私は原料メーカーに勤務した経験もあるのですが、金型、成形、原料など、あらゆる角度から工程の改善を試みることができていますし、あるひとつの問題が起きた時に、金型、成形、原料など、横断的にすべての人間で対処していくことができているのもこの会社の強みだと思います。また、大阪時代の前職に比べ、社員数が少ないこともあって、社員ひとりにかかる負担も大きいのではないかと考えたこともありましたが、まるでそんなことはなかった。それよりも、金型、成形などのそれぞれの専門家とコミュニケーションを取れることで、より円滑に仕事が進んでいるという実感もあります」
金型から成形まで一貫した生産体制をとることで現場もより精度の高い製品を製造でき、プラスチック成形品製造すべての工程で先端技術に触れ、ノウハウも溜まっていく。また櫻井は「さまざまなことをマニュアル化してノウハウを共有していきたい」とも話す。そういったことを続けてきたことでスズモトはプラスチック成形品製造のエキスパートになったのだ。
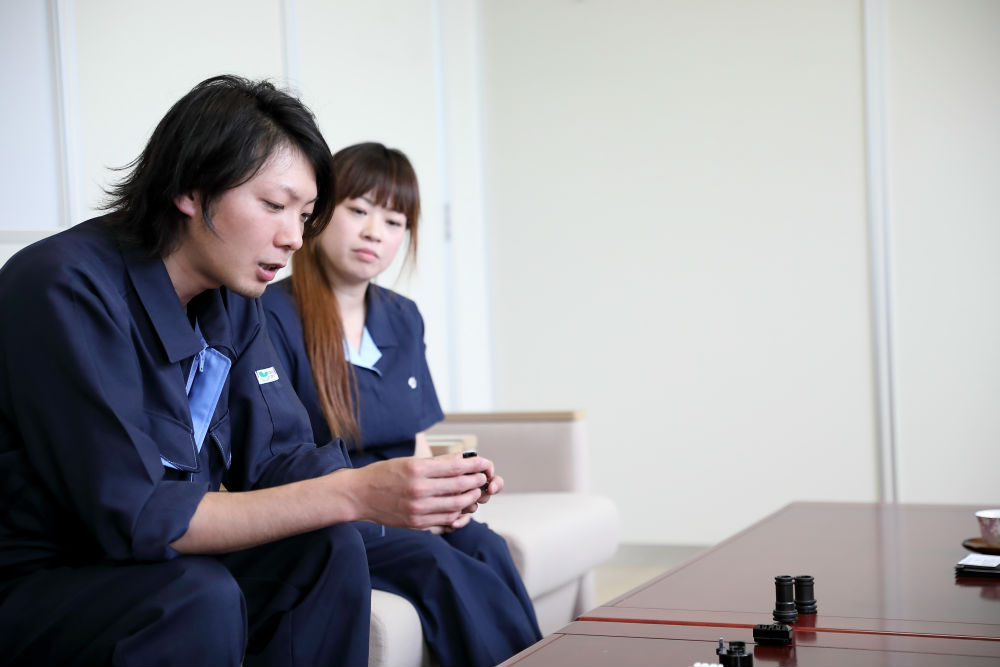
自動車車載製品の製造を手がける
現在、スズモト株式会社の主製品のひとつが売上のうちの大部分を占める自動車の車載製品だ。1980年代までは家電や日用品、OA用品などに使われる製品を主に製造していたが、1990年ごろから始まった、大手車両メーカーを中心としたトルコン用樹脂ピストンの開発プロジェクトに参加し車載部品製造が始まった。それまではアルミダイキャストで製造されていたピストンを、コストダウンや軽量化といった観点から樹脂ピストンにできないかという要望が出た。当時付き合いのあった原材料会社などから話があがり、スズモトも参加することとなった。なぜ山形の会社が参加できたのかという問いに対して、代表取締役の百瀬浩は「歴史が育んだ技術力」と答える。「もう少し詳しく言うなら、熱硬化性プラスチックに長けていたということです。家電製品に加え、様々なプラスチックの機構部品を製造していたんですね。例えば、自動車用の灰皿は火のついたものを置いたり、押し付けて消したりします。この熱にもフェノール樹脂は耐えるし、燃焼もしません。熱可塑性ではなく、熱硬化性プラスチックでないと対応できないんです。それを扱ってきた技術力が生きたんだと思います」。製造部統括係長の伊藤マリも「熱可塑性、熱硬化性の双方を扱ってきた経験とそこで育まれた技術力と経験は間違いなく当社の強みです」という。
開発の成功を機に、一時はA社向けの車載樹脂ピストンの100%を製造していた。その事業のためだけに鶴岡工場全体を使っていた時期もあるという。「しかし」と百瀬は続ける。「同じ製品を同じように作るだけでは前には進めません。樹脂という我々の分野だけでなく、自動車業界の革新にも敏感でなくてはなりません」。例えば自動車業界ではCASEが叫ばれているが、そのうちの“電製化”にも対応していかなくてはならない。より繊細な形状、より精密な精度が求められる。それでも「国内トップクラス」だという熱硬化性プラスチック製造の設備と技術でその要望にできる限り対応していく。百瀬の言葉を借りれば、それが「製造業のサポートカンパニーとしての責務」なのだ。
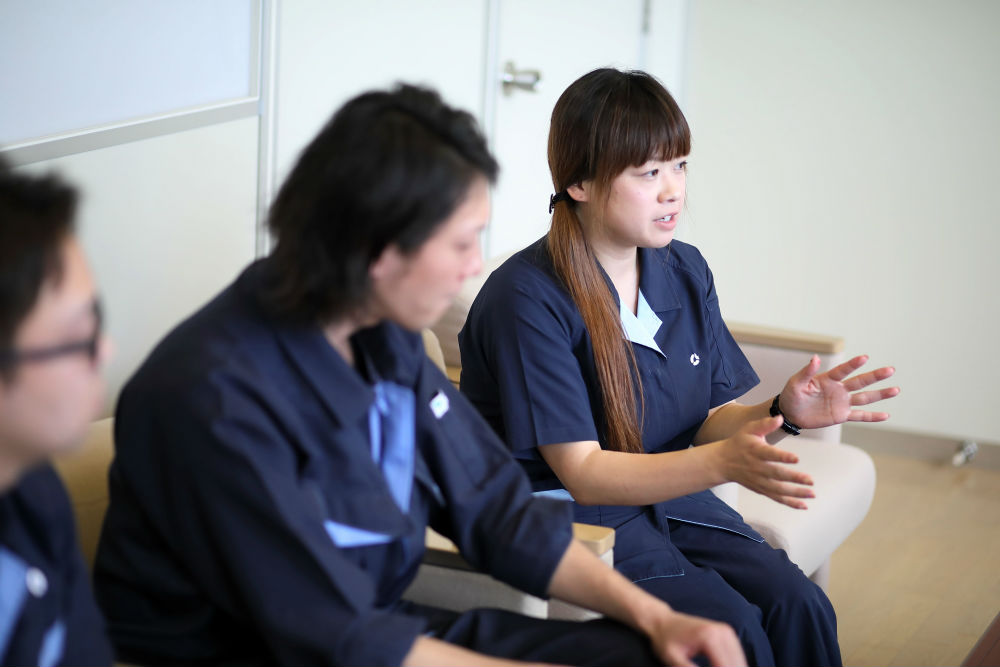
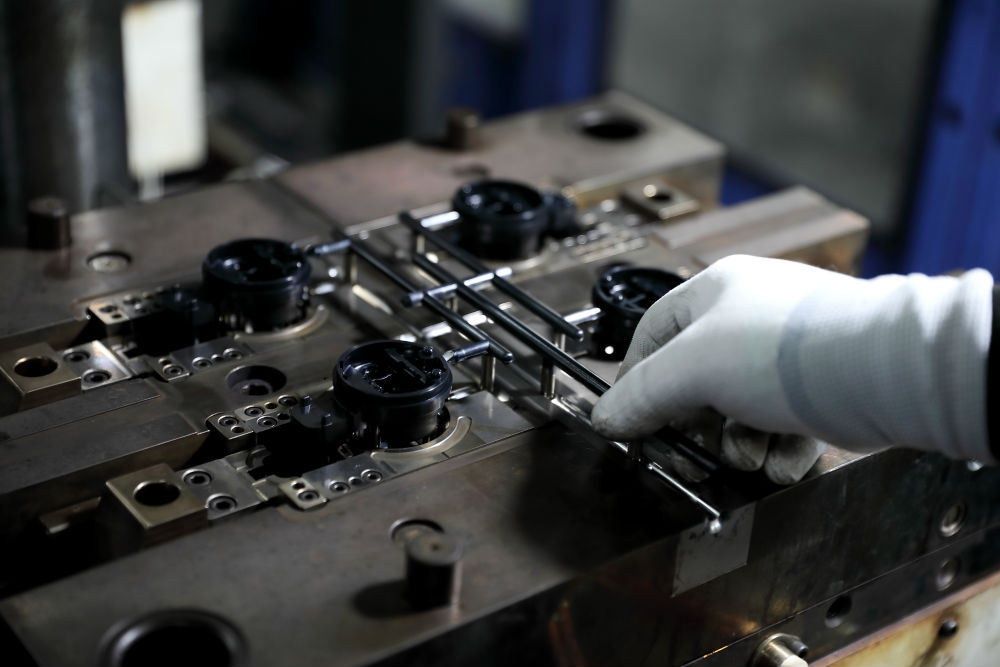
横断的なコミュニケーションから始まる仕事
今後のビジョンを百瀬に聞くと、さきほどの「サポートカンパニーとしての責務を果たす」という言葉が一番に返ってきた。それに加えて「まだ具体的な話にはなっていませんが」と前置きをおいた上でこう話してくれた。
「いわゆるアイデア商品というのでしょうか、我々の培ってきたコア技術を使った商品も作ってみたいと思っています。例えばドローンの製造に加わって、樹脂領域の仕事でできることを開発段階から加えていく。そういった商品開発ができるのではないかと」
そのほか、環境への取り組みも今後の課題だ。さきほどから挙がっている熱硬化性というのは読んで字のごとく熱で硬くなるプラスチックだ。熱に強いというメリットがある反面、熱では利用後の処理が難しいということにもなる。そこで教育機関と協業で、熱硬化性プラスチックの再利用も開発していきたいという。そのためには活発な意見交換が必要だと思うが、社内の雰囲気として伊藤は「風通しはいいと感じている」と言う。
「そもそも社長の百瀬がよく工場を回る人なんです。不安に思っていることも相談できる。そんな社長がいるというのはすごくいい環境だと思っています」。
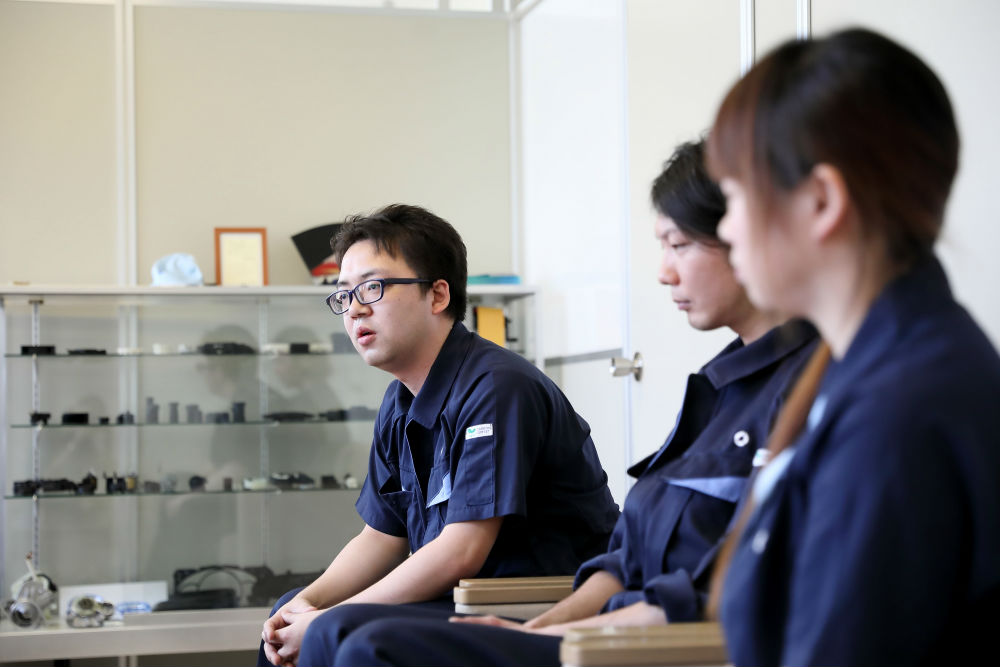
日本の製造業を内側から支える仕事。「サポートカンパニー」という言葉を使った百瀬だったが、こうも言っていた。「モルダー、つまり私たちの仕事は、モノ作りが好きな人間たちなんです。だから内側の部品だけれども、みんなそれぞれが矜持を持って“モノ作り”に携わっていると思っています」。伊藤も入社のきっかけの質問をしたときにこう話してくれた。「もともと製造業についていたのですが、仕事の領域を広げたいと思いスズモトに入社しました。専門的な知識があるわけではなかったのですが、自分たちが作っているものが街を走っている多くの車のなかに入っているんだと実感するようになりました。誇りというと大げさですが、うれしくなる瞬間はありますね」。
インタビューを行った3人がそれぞれの立場からさまざまな話をしてくれた。まさに“モノ作り”の現場を垣間見ることができたインタビューだった。
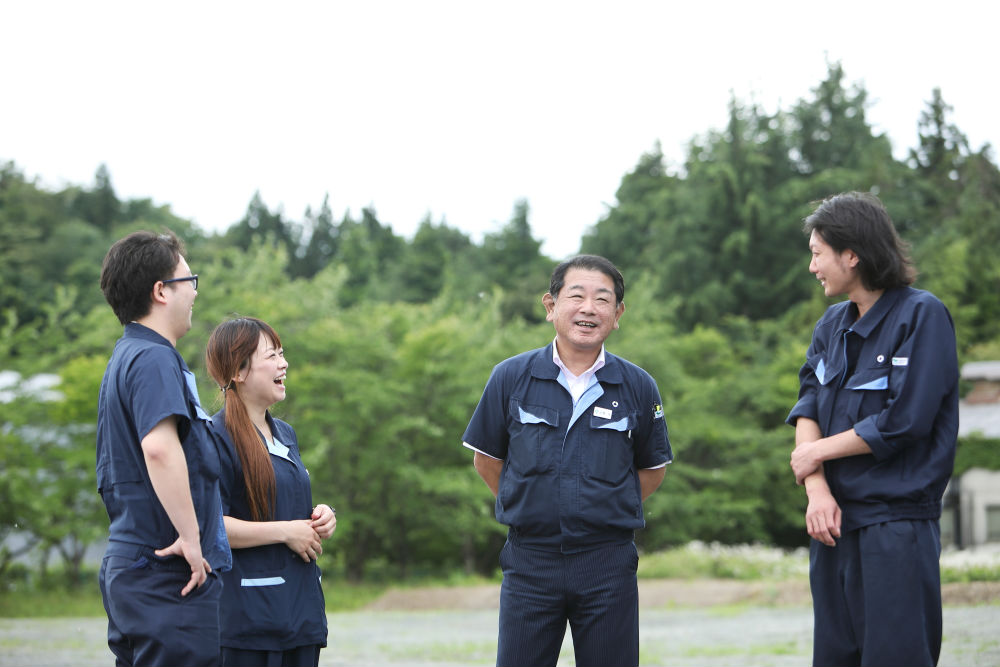